-
No. 28, Zhanqian 1st Street, Liuhua Subdistrict, Yuexiu District, Guangzhou City
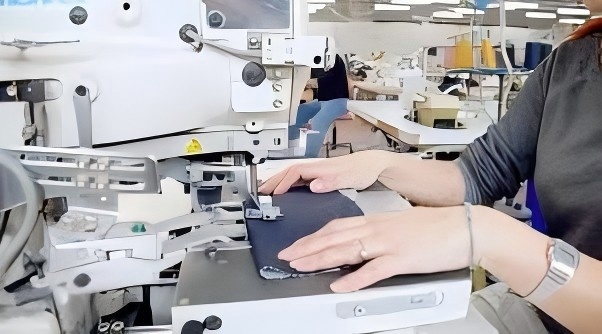
The Ultimate Jeans Manufacturing Guide: 10 Key Steps to Perfect Denim
Table of Contents
Abstract
Behind a pair of high-quality jeans is the perfect combination of textile technology and fashion design. This article deeply analyzes the 10 core links of jeans manufacturing, covering key elements such as fabric selection, weaving technology, cutting technology, washing and aging, hardware accessories, quality inspection, and explores sustainable production and future trends. By comparing industry data and process differences, you will master the method of identifying high-quality jeans and understand how to choose the style that suits you best.
1. Cotton quality determines the life of jeans
Core argument: High-quality cotton is the basis of durability
- Long-staple cotton (such as Egyptian cotton) has a fiber length of more than 35mm, which is 40% more wear-resistant than ordinary cotton
- Organic cotton reduces the use of pesticides by 60% (GOTS certification standard)
- Data comparison: The breaking strength of Xinjiang cotton reaches 28cN/tex, far exceeding the 18cN/tex of ordinary cotton
Industry case:
- Levi’s® Premium series uses Zimbabwean cotton, which extends the life of the fabric by 3 times
- Nudie Jeans uses organic cotton across the board, reducing 200 tons of chemical pollution each year
2. Dyeing process: Why is traditional indigo irreplaceable?
Core argument: Dyeing depth affects color durability
- 8-12 times of indigo dyeing can achieve authentic denim blue (color fastness above level 4)
- Sulfur black dyeing requires the addition of aniline compounds, and its environmental index is 30% lower than indigo
- Innovative technology:
- DyeCoo waterless dyeing saves 95% of water (already used by Adidas)
- Natural indigo fermentation process (traditional technique in Okayama, Japan)
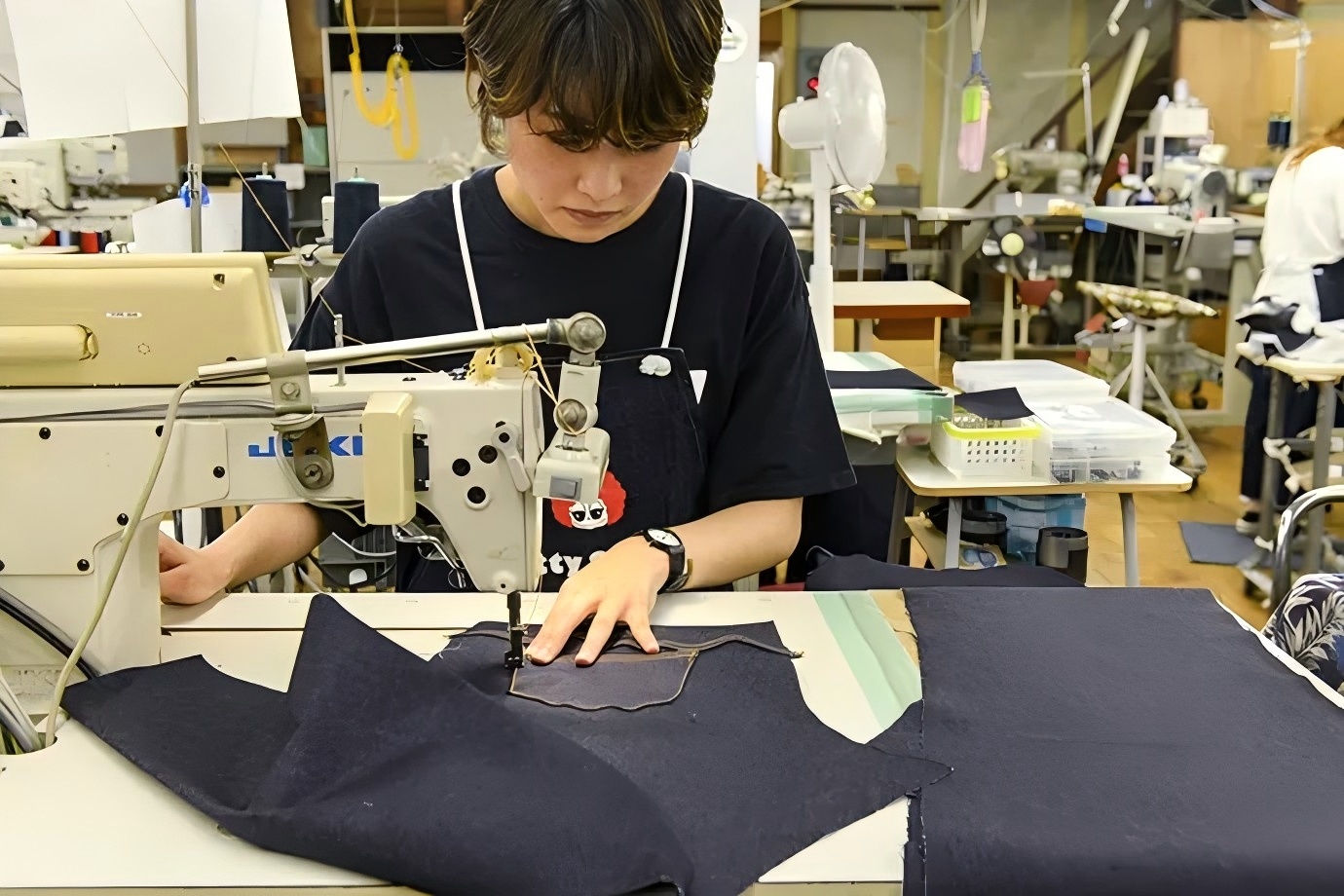
3. Weaving secrets: Why has twill become the industry standard?
Core argument: Weaving method determines fabric properties
- 3×1 twill: warp and weft ratio 3:1, 50% higher wear resistance than plain fabric
- Broken twill eliminates fabric distortion (Lee® patented technology)
- Weight standard:
- Lightweight (8-10oz): suitable for summer
- Mediumweight (12-14oz): daily wear
- Heavyweight (16oz+): special for workwear
Brand comparison:
- Wrangler® uses 13.5oz 3×1 twill, and the actual lifespan of coal miners exceeds 5 years
- Uniqlo slim fit uses 2×1 twill + 2% elastic fiber, which significantly improves comfort
4. Cutting science: How to make jeans fit different body shapes?
Core argument: Pattern design must be ergonomic
- Golden ratio: crotch length = height × 0.3 ± 1cm (Japanese EDWIN algorithm)
- Three-dimensional tailoring:
- 7-piece tailoring (Diesel® patent) enhances hip fit
- Knee pre-bend design (Lee®) reduces deformation when worn
- Error control: High-end brands allow ± 0.5cm error, fast fashion up to ± 1.5cm
Consumer data:
- 68% of consumers in the Asian market prefer mid-waist slim fit
- 42% of European and American markets prefer high-waist loose fit
5. Sewing details: invisible craftsmanship gap
Core argument: Seam strength determines service life
- Double-needle chain stitchTensile strength reaches 200N (ordinary single needle only 80N)
- Rivet process:
- Copper rivets (Levi’s® original) are highly resistant to corrosion
- Hidden rivets (APC) avoid skin friction
- Stitch length standard: 8-12 stitches/inch is the high-quality standard, and less than 6 stitches are easy to open
Destructive test:
- High-quality jeans seams can withstand 3,000 washing machine tumbles
- Fast fashion products have loose threads after an average of 500 tumbles
6. Washing revolution: environmentally friendly evolution of aging technology
Core argument: traditional technology vs modern technology
- Disadvantages of stone washing: A single pair of jeans consumes 70L of water and produces 200g of microplastics
- Laser aging:
- Accuracy of 0.1mm (Levi’s® FLX technology)
- Save more than 90% of water
- Ozone bleaching: Replace chlorine bleaching and reduce 90% of toxic substances
Process comparison: | Process type | Time | Cost | Environmental Index | |———-|——|——|———| | Hand Polishing | 45min | $3.5 | ★★☆☆ | | Enzyme Washing | 30min | $2.8 | ★★★☆ | | Laser | 8min | $1.2 | ★★★★ |
7. Hardware Accessories: The Overlooked Key to Quality
Core Argument: Details Determine the Wearing Experience
- YKK Zipper:
- Opening and Closing Test Standard: 5000 Times without Failure
- Plating Thickness ≥5μm Rust-proof
- Button Material:
- Pure Copper Button (LVC Series) Hardness of 80HRB
- Resin Buttons Reduce Weight by 40%
- Leather Label Certification:
- The Cost of Genuine Leather Label (3mm Thickness) is 6 Times That of Imitation Leather
Industry insider information:
- Nickel release from inferior metal parts is 3 times higher than the standard (EU standard ≤0.5μg/cm²/week)
8. Quality inspection: the secret weapon of high-end brands
Core argument: AQL standard determines defect rate
- Color fastness test:
- Friction test (dry/wet) reaches level 4 or above
- Light test (20 hours) discoloration ≤ level 1
- Dimensional stability:
- Sanforized shrinkage is controlled within 1%
- Non-sanforized fabric shrinkage reaches 8-10%
Quality inspection comparison: | Brand level | Inspection items | Allowable defect rate | |———-|———–| | Luxury brands | 58 items | ≤1.5% | | Fast fashion | 23 items | ≤6% |
9. Sustainable innovation: the green future of jeans
Core argument: environmental protection and performance can be achieved at the same time
- Recycled materials:
- Recycled cotton blends (Nudie Jeans® uses 30% recycled cotton)
- Fishing nets transformed polyester fiber (G-Star RAW ocean plastic series)
- Waterless process:
- Nano bubble dyeing (saving 83% water)
- Carbon dioxide dyeing (DyeCoo technology)
Industry data:
- Carbon emissions from traditional jeans production reach 33.4kg/pair
- Environmentally friendly processes can reduce to 18.7kg/pair
10. Buying guide: 5 steps to identify high-quality jeans
Core argument: How consumers can avoid IQ tax
- Tactile test: Fabrics above 14oz should be stiff and have a sense of muscle
- Seam inspection: 10 stitches per inch or more is preferred, with no more than 3 thread ends
- Hardware verification: The zipper must be engraved with YKK
- Color fading test: No obvious discoloration when rubbed with white cloth
- Pattern judgment: The front and back crotch lines should be symmetrical when laid flat
Price range analysis:
- Below ¥300: Most likely to use recycled cotton + simple sewing
- ¥800+: Usually contains long-staple cotton + double needle sewing + environmentally friendly technology
FAQS
1. What makes long-staple cotton better for jeans?
Long-staple cotton (e.g., Egyptian, Xinjiang) has stronger, smoother fibers, increasing durability by 40% compared to regular cotton.
2. Why does indigo dye fade uniquely?
Traditional indigo bonds superficially to fibers, creating gradual fading (“color loss”) with wear.
3. What’s the difference between 3×1 and 2×1 twill?
3×1 twill is denser (ideal for workwear), while 2×1 is softer (common in slim-fit jeans).
4. How to spot poor-quality stitching?
Check for loose threads, uneven seams, or fewer than 8 stitches per inch.
Summary
From cotton fields to wardrobes, a pair of high-quality jeans needs to go through 200+ processes. With the maturity of technologies such as laser aging, waterless dyeing, and degradable fibers, the jeans industry is ushering in an environmental revolution. Consumers can penetrate the marketing fog and choose products that are truly worth the money by understanding key indicators such as fabric weight, stitching density, and hardware quality.
Are you willing to pay 30% more for environmentally friendly technology? Welcome to share your views!