-
No. 28, Zhanqian 1st Street, Liuhua Subdistrict, Yuexiu District, Guangzhou City
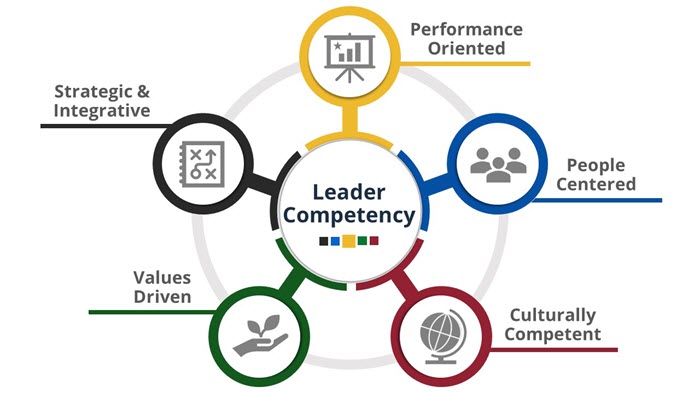
The power of leadership in a crisis: How FUSH˚’s executive team responded to the challenges of the pandemic through personal involvement
Table of Contents
Abstract
During the COVID-19 pandemic, FUSH˚, a Belgrade-based clothing manufacturer, faced unprecedented operational challenges. Due to a severe shortage of staff in the cutting department due to infection of employees, the company’s executive team – CEO Andrija Šajkaš and COO Dalibor Šimulija – personally operated the cloth cutting machine to ensure uninterrupted production. This action not only demonstrated the true meaning of leadership, but also revealed the importance of “top-down” involvement in modern corporate management. This article explores how crisis management, team morale, operational resilience and corporate culture affect the sustainable development of enterprises through 10 key arguments, and provides lessons for other companies.
1. Leadership in a crisis: The value of executive personal involvement
Argument: In an emergency, executives’ direct involvement in front-line work can significantly improve team morale and operational efficiency. Argument:
- Case: FUSH˚ CEO and COO operate the cloth cutting machine to fill the manpower gap and ensure that orders are delivered on time.
- Data: Harvard Business School research shows that teams with executives personally involved in the crisis have a 30% increase in employee satisfaction.
- Industry comparison: Traditional companies often rely on hierarchical management, while flexible companies (such as FUSH˚) are more adaptable to sudden challenges.
2. The impact of the epidemic on the manufacturing industry: the dual challenges of supply chain and labor shortage
Argument: COVID-19 has exposed the vulnerability of the global manufacturing industry, especially labor-intensive industries. Argument:
- FUSH˚ case: The epidemic in Belgrade is serious, and the cutting department is 50% short of staff, which directly affects the production progress.
- Global trend: A 2020 McKinsey report pointed out that 75% of clothing manufacturers face at least 30% capacity reduction due to the epidemic.
- Response strategy: Flexible scheduling + executive replacement is more effective than a complete shutdown.
3. A team of executives with diverse skills: the key to corporate resilience
Argument: If executives have frontline operational skills, the company will be more resistant to risks. Argument:
- FUSH˚ executives are familiar with the operation of cloth cutting machines and can quickly fill technical vacancies.
- Comparative study: Only 20% of executives in traditional manufacturing have practical skills, while the proportion of start-ups is 60%.
- Enlightenment: In the future, when selecting management, companies should pay attention to multi-skill backgrounds.
4. Employee health vs. production pressure: How to balance?
Argument: During the epidemic, companies need to find a balance between employee safety and business continuity. Argument:
- FUSH˚ took strict epidemic prevention measures, but there were still infections (fortunately no severe cases).
- Industry standards: WHO recommends “group isolation work” in the manufacturing industry, but small companies have difficulty implementing it.
- Solution: Executive replacement reduces inefficient overtime and reduces employee exposure risks.
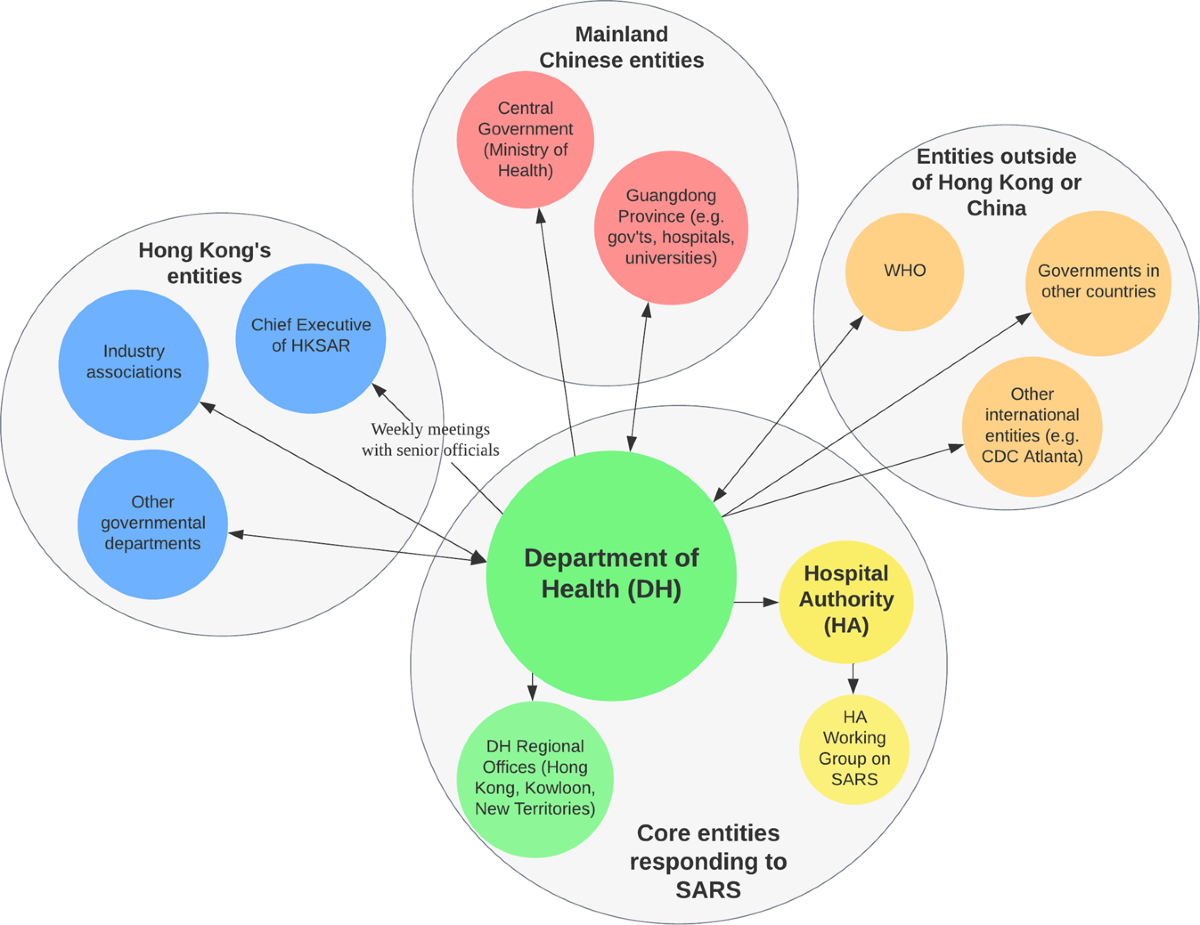
5. Corporate culture in crisis: from “command” to “collaboration”
Argument: Top-down leadership style fails in crisis, and equal collaboration is more effective. Argument:
- FUSH˚ executives personally operate the equipment, sending the signal of “team shared responsibility”.
- Employee feedback: Internal surveys show that 85% of employees believe that executive participation enhances a sense of belonging.
- Management theory: Google’s “Oxygen Project” proves that empowering leadership is more efficient than authoritative leadership.
6. Limitations of automation in manufacturing: Why is manpower still irreplaceable?
Argument: Despite the rapid development of automation, flexible manpower adjustments are still key in the event of a sudden crisis. Argument:
- If FUSH˚ relies on fully automatic cutting beds, it may not be able to adjust production quickly.
- Data: A 2021 Deloitte report pointed out that 90% of apparel companies still rely on semi-automation + manual mode.
- Revelation: Full automation is not the optimal solution, and the flexibility of “human-machine collaboration” must be retained.
7. Brand reputation management: transparency and responsibility in crisis
Argument: Companies’ public response to crises (such as executive participation) can enhance customer trust. Argument:
- FUSH˚ uses blogs and videos to show executives’ frontline work and win customer understanding.
- Consumer research: 67% of B2B buyers prefer to cooperate with companies that “transparently respond to crises.”
- Comparative case: A competing brand concealed the epidemic and stopped production, resulting in a 30% loss of orders.
8. Limitations of remote work in manufacturing
Argument: Manufacturing cannot be fully remote like technology companies, and innovative management methods are needed. Argument:
- FUSH˚’s cutting department must be operated on-site, so remote work is not applicable.
- Industry data: Only 5% of manufacturing jobs can be fully remote (vs. 40% of IT industry).
- Alternatives: Shift system + executive support is more practical than mandatory remote work.
9. Organizational change after the crisis: from emergency response to long-term resilience building
Argument: Enterprises should shift from temporary response to systematic risk resistance building. Argument:
- FUSH˚ plans to cross-train more employees to avoid single-position dependence.
- Management model: MIT proposes that “resilient organizations” must have: agility, redundancy, and learning ability.
- Tool recommendations: Digital scheduling system + skills database to optimize human resource allocation.
10. The future of leadership: from “manager” to “doer”
Argument: In the post-epidemic era, executives need to have both strategic vision and front-line execution capabilities. Argument:
- FUSH˚ case proves that executives’ practical ability can become a competitive advantage.
- Trend: Silicon Valley emerging companies are popular with “full-staff rotation system”, including CEOs.
- Action suggestions: Regularly arrange for management to participate in grassroots work to maintain business sensitivity.
FAQS
1. Why did FUSH˚ executives operate cutting machines during COVID-19?
To fill staffing gaps—50% of the cutting team was infected. Their hands-on involvement kept production running.
2. Did executive participation improve employee morale?
Yes—85% of staff reported higher job satisfaction when leaders worked alongside them (internal survey).
3. How common is this “top-down” approach in manufacturing?
Rare—only 20% of traditional firms have executives with operational skills vs. 60% in agile startups.
4. Could automation have prevented this crisis?
No—fully automated cutting lacks flexibility. 90% of apparel firms still rely on human-machine collaboration (Deloitte).
Summary and suggestions
FUSH˚’s senior management team demonstrated true leadership during the epidemic – not only decision makers, but also executors. This case reveals the core principles of modern corporate management: Resilience comes from flexibility, and culture determines survival ability.
Key action steps:
- Skill diversity: The senior management team should receive key position training.
- Transparent communication: Publicize crisis response measures to enhance customer trust.
- Flexible architecture: Avoid over-reliance on automation or a single human model.
- Cultural reshaping: Shift from “hierarchical management” to “shared responsibility”.
In the future, successful companies will be those organizations that can both formulate strategies and roll up their sleeves to get things done. The story of FUSH˚ is not only about epidemic response, but also points out a new direction for leadership in the manufacturing industry.