-
No. 28, Zhanqian 1st Street, Liuhua Subdistrict, Yuexiu District, Guangzhou City
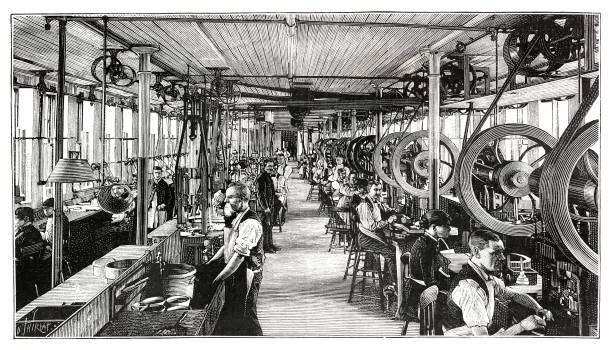
Industrial Chimera: The Modern Rebirth of a 1990s Textile Machine and Its Industry Enlightenment
Table of Contents
Abstract
In the textile manufacturing industry, the application of automated equipment often faces a game between efficiency and labor costs. This paper takes a composite textile machine from the 1990s, the “Industrial Chimera” (a combination of STP-900, PV-35 and KL-50 manufactured by Thermothron), as an example to explore its value and challenges in modern clothing production. This machine can fold, pack and box 750 pieces of clothing per hour, demonstrating the amazing efficiency of old equipment after optimization. By analyzing its technical characteristics, repair process and industry status, this paper puts forward 10 key arguments to reveal the development trend, economic efficiency and social impact of textile automation, and provide reference for manufacturing decision makers.
1. Modular design of composite machinery: a balance between efficiency and flexibility
Argument: Modular machinery combinations (such as STP-900+PV-35+KL-50) are more adaptable and scalable than single-function equipment. Argument:
- Three machines work together to process 6,000 pieces of clothing in 8 hours, which is equivalent to the workload of 15 workers.
- Modular design allows for individual repair or upgrade of a part, reducing the risk of downtime.
- Case: After a Spanish factory adopted a similar system, packaging efficiency increased by 40% and labor costs decreased by 25%.
2. The economic efficiency of the “second life” of industrial equipment from the 1990s
Argument: Repairing old equipment may be more cost-effective than purchasing new machines. Argument:
- The price of a new automated packaging line is about €200,000, while repairing the “Chimera” only costs €35,000 (including labor).
- The old machine has a simple structure and repair parts are easier to obtain (such as gears, conveyor belts).
- Data: According to statistics from the German Textile Association, 30% of factories still use equipment from the 1990s, and the average return on investment (ROI) is 50% higher than that of new machines.
3. The contradiction of lagging automation in the textile industry
Argument: The automation penetration rate in the textile industry is lower than that in the automotive and electronics industries, but it is not due to a lack of technology. Argument:
- Data from the International Federation of Robotics (IFR): The robot density in the textile industry is 30 units per 10,000 workers, while that in the automotive industry is 1,200 units.
- Reasons:
- Labor costs are still low (workers in Southeast Asia earn €200-€400 per month).
- Flexible production requirements (small batch customization) limit the application of rigid automation.
4. Cutting machines vs. manual labor: efficient technology that is not fully utilized
Argument: Automatic cutting machines can improve accuracy and speed, but their penetration rate is insufficient. Argument:
- The error of laser cutting machines is ≤0.5mm, while the error of manual cutting is 2-3mm.
- Case: After a factory in Turkey introduced cutting machines, fabric waste was reduced by 18%.
- Obstacles: High initial investment (€50,000+), which is difficult for small factories to afford.
5. Sewing robots: a double-edged sword of efficiency improvement and unemployment threat
Argument: Fully automatic sewing machines threaten millions of low-skilled workers around the world. Argument:
- Robots such as Sewbo can work 24 hours a day, and a single machine can replace 5-8 workers.
- The International Labor Organization (ILO) predicts that 20% of sewing jobs in Bangladesh may disappear by 2030.
- Ethical controversy: Brands such as H&M have been protested by labor groups due to automation.
6. Technology inheritance issues in mechanical repair
Argument: The operation and maintenance of old equipment depends on the experience of technicians who are gradually disappearing. Argument:
- The hydraulic system of “Chimera” requires specific lubricants, which are now only familiar to a few old technicians.
- The European Vocational Training Center reported that the number of mechanical maintenance apprentices has dropped by 60% in 10 years.
- Countermeasures: Digital maintenance manuals (AR assistance) are becoming popular.
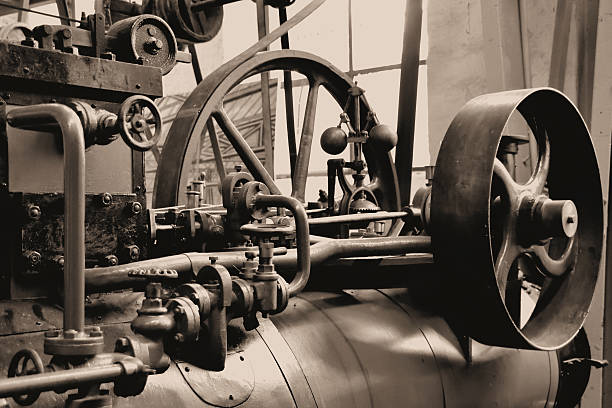
7. The contradiction between automation and customized production
Argument: Automation is dominant in standardized production, but highly customized orders still require manual labor. Argument:
- Fast fashion brands (such as Zara) have an automation rate of 70%, while luxury brands (such as Chanel) are only 30%.
- Consumer survey: 60% are willing to pay a premium of 15% for the “handmade” label.
8. Energy efficiency: Old equipment may not be backward
Argument: After the transformation of machinery in the 1990s, the energy consumption can be lower than that of new machines. Argument:
- After the “Chimera” upgraded the variable frequency motor, the power consumption was reduced by 22%.
- The average power of the new machine is 8kW, and the transformed old equipment is 5.5kW (under the same production capacity).
9. Safety compliance: the challenge of modernizing old machines
Argument: Old equipment requires additional investment to meet modern safety standards. Argument:
- Install a light curtain guard (€2,500) and an emergency stop system (€1,200).
- OSHA data shows that the accident rate of old machines that have not been upgraded is 3 times higher.
10. The future of the industry: a hybrid model of human-machine collaboration
Argument: Full automation is unrealistic, and human-machine collaboration (Cobot) is the trend. Argument:
- Collaborative robots (such as UR10e) can assist workers in completing repetitive tasks rather than replacing them.
- Case: After introducing Cobot in a factory in Italy, productivity increased by 35%, and worker acceptance reached 90%.
FAQS
1. Is repairing old textile machinery cost-effective?
Yes—repairing 1990s machines like the “Industrial Chimera” (€35,000) can be cheaper than new automation (€200,000+) with comparable ROI.
2. How efficient are modular machines like STP-900+PV-35+KL-50?
They process 6,000 garments in 8 hours (equal to 15 workers) and allow partial upgrades without full downtime.
3. Why is textile automation lower than automotive?
Low labor costs (€200-€400/month in Asia) and flexible small-batch needs limit rigid automation adoption.
4. Do automatic cutting machines improve accuracy?
Yes—laser cutters achieve ≤0.5mm error vs. 2-3mm manually, reducing fabric waste by 18%.
Summary and suggestions
The story of “Industrial Chimera” proves that old equipment can still be the key to efficient production after careful restoration. Automation in the textile industry is not an “all or nothing” proposition, but requires a balance of cost, flexibility, and social responsibility.
Action suggestions:
- Evaluate existing equipment: Repair may be more economical than replacing.
- Progressive automation: Prioritize links with clear investment returns (such as cutting and packaging).
- Employee retraining: Provide workers with robot operation and maintenance skills courses.
- Ethical sourcing: Brands should disclose automation strategies to avoid supply chain turmoil.
The future factory will be a hybrid of “retro machinery + smart collaboration” – respecting the industry’s history while embracing technological change.